Obsolescence Management for Electronic Components
Electronics Design
Electronics Design Entrust your new application to our world-class electronics engineers
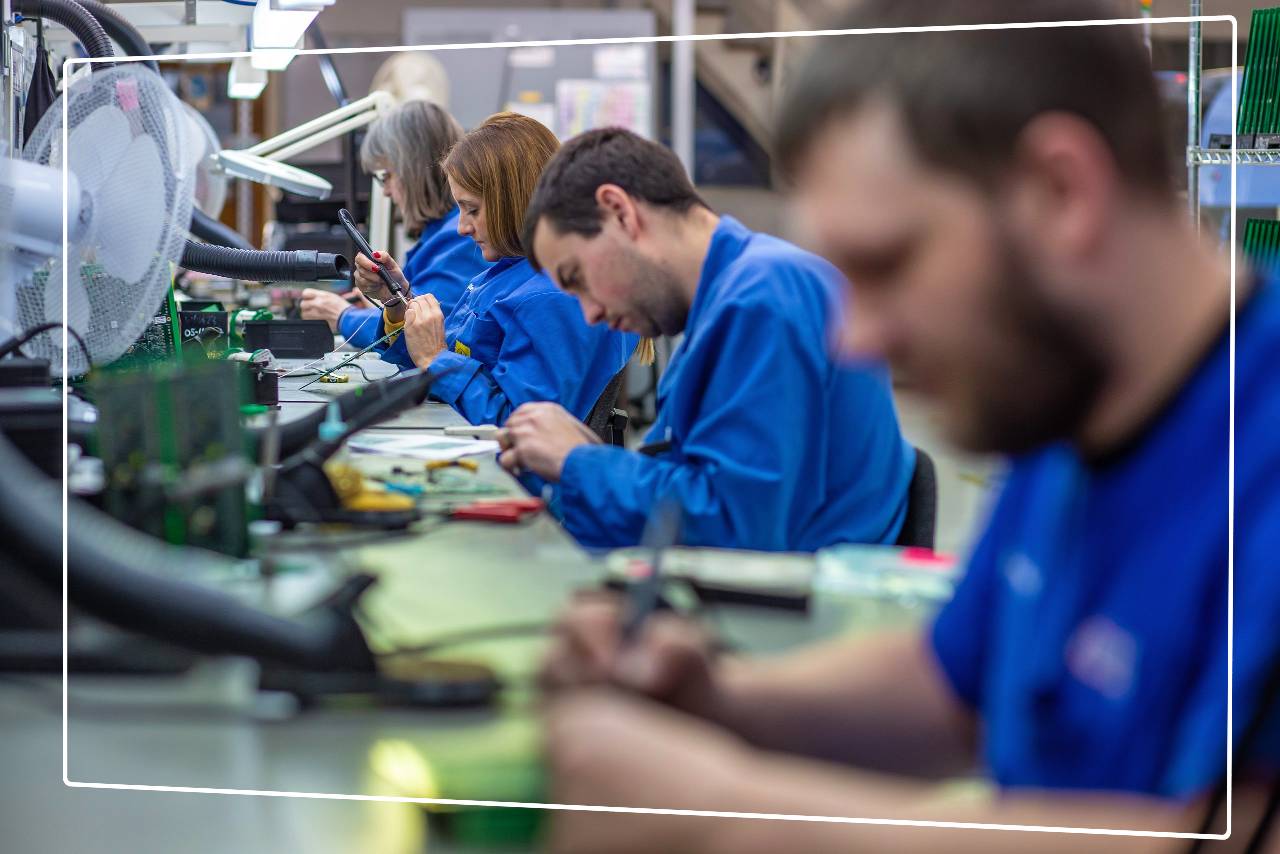
Obsolescence checks are critically important in manufacturing because they help to ensure that the parts and components used in the production process are still viable and available. In manufacturing, components can become obsolete for a variety of reasons, including changes in technology, market demand, and regulation. Without proper obsolescence checks, manufacturers may unknowingly continue to use outdated parts and components, which can result in decreased efficiency, increased costs, and even product failure.
By regularly checking for obsolescence, manufacturers can proactively identify and address potential issues before they become major problems, ensuring that their products remain reliable and competitive in the marketplace.
Consider obsolescence on your Bill of Materials to avoid:
- Production delays: If an essential component becomes obsolete, it can cause delays in the production process as the company scrambles to find a replacement.
- Increased costs: Obsolete components can be more expensive to source, or require redesigning the product, which can drive up costs.
- Product failure: If a company continues to use obsolete components in their products, it can lead to product failure, customer dissatisfaction, and potential liability issues.
- Damage to company reputation: Product defects and failures can seriously impair a company's reputation, making it difficult to recover from the loss of trust.
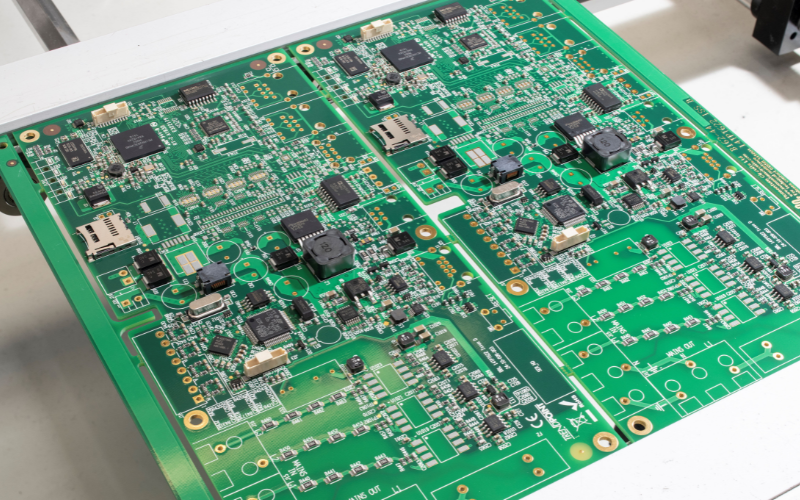
How our parts obsolescence services work
Most contract manufacturers in the UK don’t have a full engineering team so aren’t qualified or capable of providing a solution to parts that are obsolete. They will simply push the problem over to you to solve. We won’t. We work in two ways, depending on who the design authority is:
- BitBox as the design authority: The engineering team will be notified of the PCN (product change note) from the end manufacturer of the component and will immediately begin identifying suitable alternatives. We will begin with looking for footprint-compatible devices to avoid any PCB respins, but if that isn’t an option, we will then identify a component that is fit for purpose, offers the correct level of tolerance, and requires the minimum amount of changes necessary without negatively impacting performance. You are merely being kept in the loop and all decisions (and responsibility) sit with BitBox.
- You as the design authority: Despite BitBox not designing the product, when we receive notification of the PCN, we will still go through a similar process detailed above. We won’t throw the problem to you and wash our hands of it. We’ll communicate the problem but also work with you (if required), to suggest suitable alternatives. The main difference to the above is we’re suggesting alternatives for the design authority to then validate and sign off on.